-
Welcome to 205GTIDrivers.com!
Hello dear visitor! Feel free to browse but we invite you to register completely free of charge in order to enjoy the full functionality of the website.
-
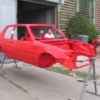
[Car_Restoration] My 1989 205 1.9 Gti Restoration Project
By
mrfirepro, in Car Restorations, Overhauls & Upgrades