-
Welcome to 205GTIDrivers.com!
Hello dear visitor! Feel free to browse but we invite you to register completely free of charge in order to enjoy the full functionality of the website.
-
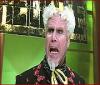
[trackday_prep] My 205 Xt Trackcar Project
By
swordfish210, in Trackday & Race/Rally Prep